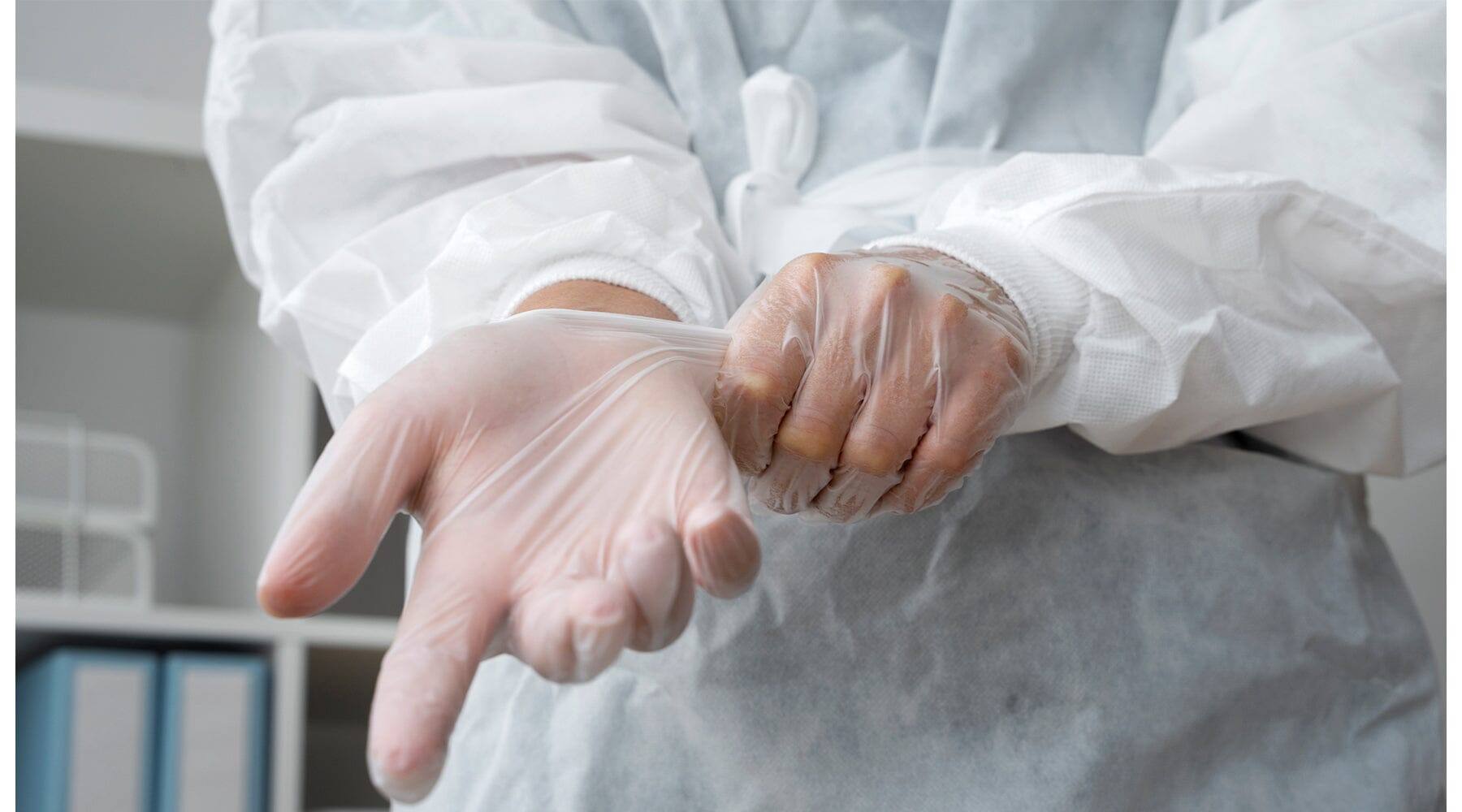
How Polyethylene Gloves Are Made
Like polyvinyl chloride (PVC), polyethylene was first created by accident. German chemist Hans von Pechmann made the first polyethylene in 1898, and in 1933 Reginald Gibson and Eric Fawcett also accidentally created polyethylene. Polyethylene is a non-leaching plastic in its natural state, so it does not release unwanted chemicals into food. This is the reason why polyethylene gloves are most suitable for the food service industry.
What Are Polyethylene Gloves Made From?
Polyethylene is a polymer that is synthesized from ethylene, and it is a thermoplastic that is formed into various shapes as it cools from a liquid to a solid state. There are different forms of polyethylene, with one being high-density polyethylene (HDPE), which is the harder and stiffer form. Low-density polyethylene (LDPE) is thinner, and more flexible than HDPE. Polyethylene is used to make plastic grocery bags, dispensing bottles, and disposable gloves. Polyethylene is a flexible and tough material, but it is not as durable as nitrile, vinyl, or latex.
How Are Polyethylene Gloves Made?
The process of making polyethylene gloves is much simpler than the process for making nitrile, vinyl, or latex gloves. Two polyethylene sheets are shaped, then they are simply seamed and sealed together with heat to create disposable gloves. Because poly gloves do not need to undergo a dipping process the way nitrile, vinyl, or latex gloves do, their manufacture is simpler and cheaper. But because they do not undergo any dipping process, polyethylene gloves are not impervious to liquids.
How Are Polyethylene Gloves Tested?
This test method designed to detect holes in food service gloves made of polyethylene that may compromise the barrier quality of the glove is the Test Method D5151. This test method is designed for use as a quality reference for holes in polyethylene food service gloves and for manufacturers to evaluate the ongoing control of holes in food service gloves made of polyethylene. A mandrel is mounted in a vertical position using suitable clamps or hangers. The glove is attached to the mandrel by stretching the cuff of the glove around the mandrel. A maximum of 40 mm of the glove cuff should fit over the bottom end of the mandrel. A securing device is used to hold the glove in place. The remaining part of the glove is allowed to hang freely and then filled with water. A minimum of 1000 cubic centimeters of water having a temperature of 15 to 30°C is poured into the top of the mandrel. Finally, the glove is inspected visually for immediate water leakage and the test is repeated after 2 minutes.
Leave a comment